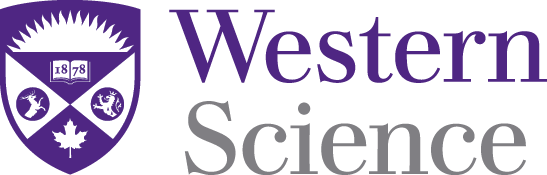
Chemistry Publications
Document Type
Article
Publication Date
12-2023
Journal
Additive Manufacturing Letters
Volume
7
URL with Digital Object Identifier
https://doi.org/10.1016/j.addlet.2023.100156
Abstract
Ti6Al4V has been used widely as a biomedical alloy and is increasingly manufactured by additive manufacturing due to customized shapes. As implant material, it is frequently exposed to both friction and corrosive environments. This study investigates the effect of the fabrication process (laser powder bed fusion and forging) on the tribocorrosion behavior of Ti6Al4V in various environments including diluted hydrochloric acid to simulate the acidic environment in a crevice (HCl), phosphate-buffered saline (pH 7.3) with 10 g/L bovine serum albumin (PBS+BSA), and PBS+BSA with 30 mM H2O2. While the presence of BSA hindered the repassivation (reforming of the protective passive surface oxide), the presence of H2O2 accelerated it. HCl resulted in a localized tribocorrosion process. The highest plastic deformation rate was found in the PBS+BSA solution followed by HCl and PBS+BSA+H2O2. In addition, AM parts presented a higher microhardness and smaller grain sizes compared to forged materials. There was no influence of the manufacturing process on the coefficient of friction (COF) in HCl and PBS+BSA solutions, however, a significantly higher COF was found for forged samples in PBS+BSA+H2O2 than AM samples. Tribocorrosion was more extensive for forged than AM Ti6Al4V in all solutions.
Creative Commons License
This work is licensed under a Creative Commons Attribution-Noncommercial-No Derivative Works 4.0 License.